在工業(yè)領(lǐng)域中,橡膠密封圈作為關(guān)鍵的密封元件,其性能和壽命直接關(guān)系到機械設(shè)備的安全性與可靠性。然而,實際應(yīng)用中,橡膠密封圈常因多種原因失效,導(dǎo)致泄漏、機械故障甚至設(shè)備損壞。本文將深入探討橡膠密封圈失效的主要原因,并提出相應(yīng)的應(yīng)對措施。
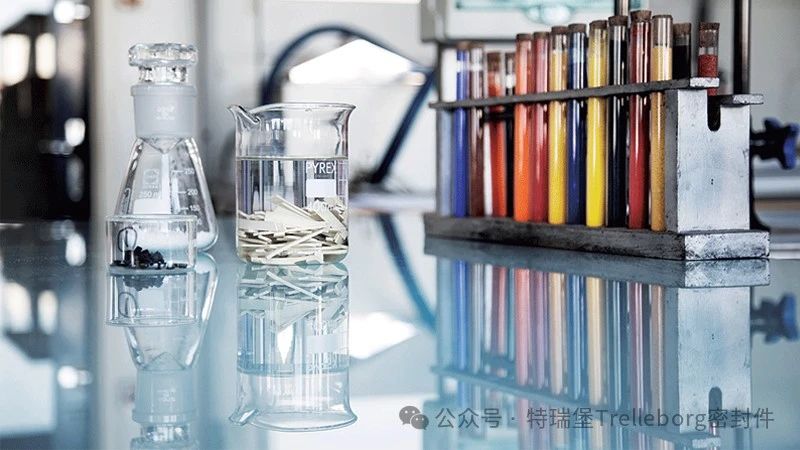
一、材料因素
橡膠密封圈的性能高度依賴于所選材料的物理、化學(xué)特性及其與工作介質(zhì)的相容性。材料選擇不當(dāng),密封圈可能因化學(xué)和機械作用而失效。材料不相容:橡膠材料需與介質(zhì)及工作環(huán)境相適應(yīng)。若不相容,可能出現(xiàn)溶脹、溶解、硬化、軟化、降解或分解等問題。
材料老化:長期使用中,橡膠會因熱、氧、臭氧、紫外等老化因素導(dǎo)致性能下降。
添加劑遷移:橡膠中的增塑劑、防老劑等添加劑可能因高溫、介質(zhì)作用遷移到表面,改變橡膠性能。
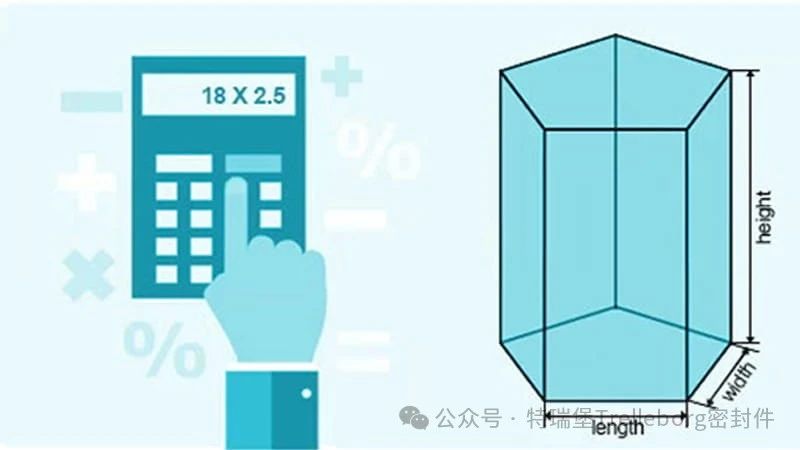
二、設(shè)計因素
設(shè)計不合理可能導(dǎo)致橡膠密封圈密封性能不足甚至失效。- 密封結(jié)構(gòu)設(shè)計:過度壓縮可能導(dǎo)致永久變形或撕裂,壓縮不足則無法形成有效密封。應(yīng)力集中設(shè)計會造成密封圈易損。
- 公差匹配:公差不合理可能導(dǎo)致密封圈無法有效貼合,過松或過緊均影響密封效果。
- 截面尺寸選擇:截面尺寸過小無法承受高壓,過大則增加裝配難度和摩擦損耗。
- 動態(tài)條件忽略:未充分考慮運動狀態(tài)下的密封要求,可能導(dǎo)致摩擦過大或耐磨性不足。
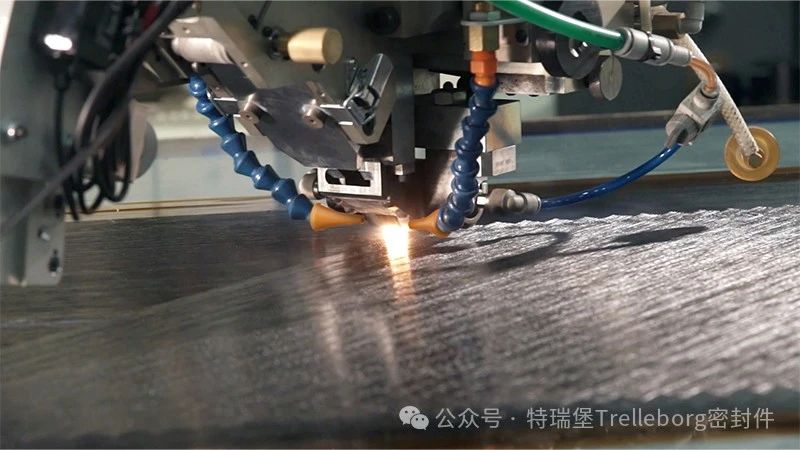
三、加工及制造因素
密封圈制造過程中的工藝問題也是失效的重要原因。
- 材料配方:配方設(shè)計不當(dāng)可能導(dǎo)致密封圈性能不達標(biāo)。
- 硫化工藝:硫化不足彈性不夠,硫化過度則脆性增加或老化加速。
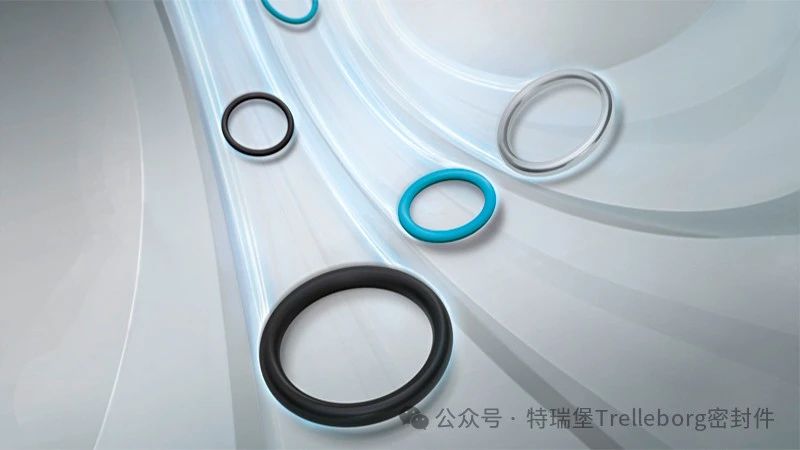
四、使用條件因素
橡膠密封圈在實際應(yīng)用中的失效與使用條件密切相關(guān)。
- 溫度超限:超出適用溫度范圍導(dǎo)致性能急劇下降。
- 壓力過高或波動:高壓環(huán)境下密封圈可能擠出或變形,壓力波動導(dǎo)致疲勞破壞。
- 運動速度和摩擦:高速度或頻繁運動導(dǎo)致磨損、老化或過早失效。
- 工作介質(zhì)污染:含有顆粒物或雜質(zhì)的介質(zhì)引起密封圈表面磨損或劃傷。
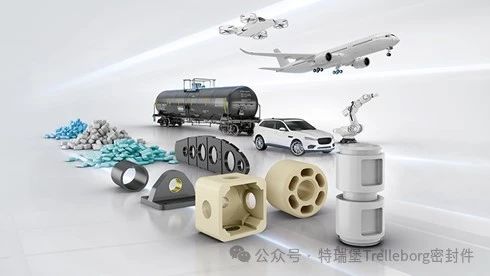
五、外界環(huán)境因素
外界環(huán)境條件對橡膠密封圈的使用壽命和性能也有重要影響。
- 化學(xué)介質(zhì)侵蝕:腐蝕性化學(xué)物質(zhì)導(dǎo)致分解或性能下降。
- 顆粒污染物:外界顆粒污染嵌入密封面造成劃傷或磨損。
- 電化學(xué)作用:特殊環(huán)境下的電化學(xué)反應(yīng)加速橡膠老化或損壞。
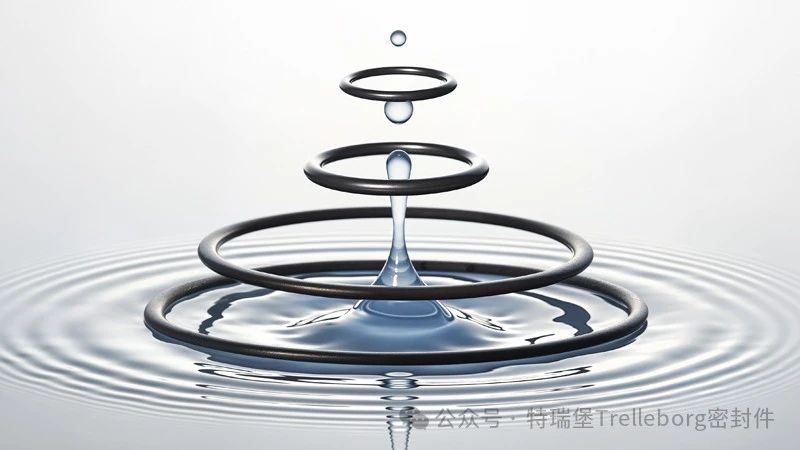
六、應(yīng)對措施
為降低橡膠密封圈失效風(fēng)險并延長使用壽命,應(yīng)采取以下措施:
- 材料優(yōu)化:根據(jù)使用環(huán)境選擇合適的橡膠材料。
- 合理設(shè)計:考慮壓縮率、公差配合、應(yīng)力分布及動態(tài)密封要求。
- 嚴(yán)格加工控制:提高加工精度,優(yōu)化硫化工藝,避免表面缺陷。
- 優(yōu)化使用條件:控制溫度、壓力和工作介質(zhì)清潔度。
- 定期維護與更換:定期檢查密封圈老化或磨損情況,及時更換失效密封圈。
綜上所述,橡膠密封圈的失效是多因素綜合作用的結(jié)果。通過綜合考慮上述因素并采取有效措施,可以顯著提高橡膠密封圈的可靠性和使用壽命,從而保障機械設(shè)備的安全運行。